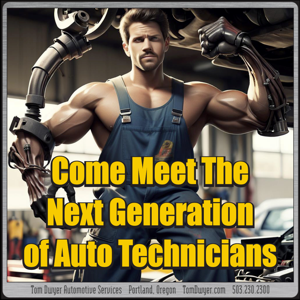
“Almost” Tom Dwyer Service is NOT Tom Dwyer Service!
“It’s never enough”, mourned Tom Dwyer, owner of the premiere independent auto repair shop in Portland. “We keep hiring the best in the business but our clients keep demanding more. It just never seems to be enough! But now there’s A.I., and it may save us all!”
“Our people have been the backbone of our business for over 40 years. I’ve always believed if you hire the best people, give them the best tools, then pay them well and treat them with respect, they’ll produce results to brag about,” Tom said. “But let’s face it… 40 years is a long time, and treating people right may be an outdated philosophy. Technology has moved on and I’m told people are becoming obsolete. Maybe I’ve been wrong all this time, so we’ve been looking into AI to handle our staffing going forward.”
We started our search by going to some of biggest AI programs and asking what the next generation of automotive technicians would look like. The results were… um… surprising. These first guys weren’t a completely bad start. The first two have Popeye forearms that say they could do the heavy lifting. The tools growing from their fingertips certainly shows their dedication, and the third guy’s hand even blends in to become part of the car! But all of them were just too darn happy for Tom. “I like auto repair as much or more than the next guy”, he said, “but anyone working in an auto shop and smiling THAT big? Says ‘drugs’ to me. Next!”
The second batch was even more encouraging. The serious looks of serious Technicians replaced the smiles, and the fact that two of them are using the same tools at the same time speaks to the very high degree of teamwork we depend on. “I’m very excited about the ability of one Tech to stand inside the engine bay while he works, and the ability for another to grow an extra arm. Those could both be big advantages!” But apparently in the future all Technicians are nearly identical early-30’s white guys with short hair and tight beards. That could make it hard to tell them apart in a day-to-day working situation.
We asked for several more examples of future technicians, but AI’s preference for young white men with scruffy beards (or occasionally older white men with reassuringly grey hair) in the profession was pervasive. In keeping with Tom’s woke DEI goals he asked to see some diversity and what we got was diverse indeed. The first young lady was particularly interesting because her 3-jointed arm would be very useful in retrieving parts dropped into inaccessible parts of an engine. We were ready to make an offer to the second woman but, unfortunately, she had to leave for an audition on an adult-oriented anime website. The last two gentlemen were also interesting; they had the extra arms and extra joints that Techs of the future will apparently need. As of press time, though, they hadn’t returned our calls.
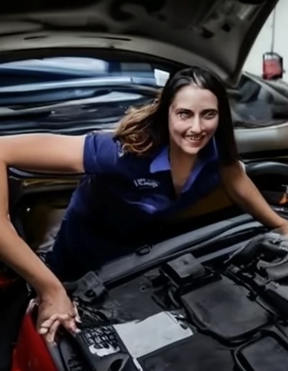
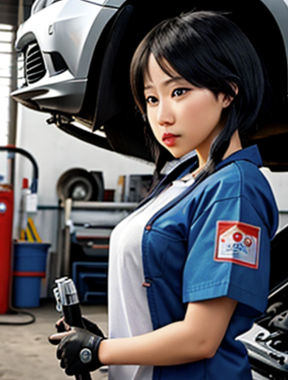
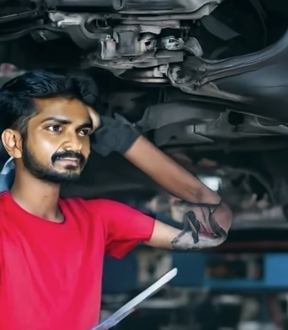
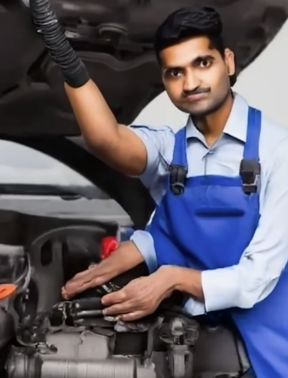
“We’re still just getting people”, Tom complained. “AI is supposed to be about a future of unlimited possibilities. Where are the mutants? WHERE ARE THE MUTANTS?!!” When the Boss asks we try to deliver, but AI includes cultural assumptions in its creations. In today’s gun-worshipping society our first search for ‘auto technicians with extra arms’ resulted in… armed technicians. Possibly useful, who knows, but not quite what we’re looking for right now.
Adding a ‘no guns’ term brought us our last two possible contenders. They both look like they’d be assets to the shop, but on the other hand (get it?) they also look like they might try to rebel against their human oppressors at any moment. Not good for shop morale!
All in all, our experience with AI staffing was a disappointment. “Fine!” said Tom. “We’ll stick with what’s been working for decades. We’ll hire the best, like Jamie, who just got one of the cutting edge hybrid/electric certifications, or Chris, who helped create the curriculum to train the next generation of technicians, or Eric, who was just recognized as Technician of the Year. We’ll make sure they’re either ASE-Certified or, better yet, ASE-Master-Certified. We’ll pay them hourly instead of industry-standard Flat Rate so they’ll be incentivized to produce quality rather than quantity, and then let the TECHS determine what the vehicles need. We’ll pair them with non-commissioned Service Advisors who’ll explain and prioritize their recommendations for the clients, then do all the parts ordering and billing that NO Technician wants to do! Our clients can tell the difference already, so we’ll just have to trust that cutting edge technology can keep up with us!”